Woodworking is a craft that requires precision and skill. It involves various cuts that shape and size lumber, making it suitable for functional and artistic projects.
When cutting your lumber, contact a reputable industrial lumber supplier like Alderfer. They use machine tools to cut wood products that are more accurate and precise than hand cutting. Click Custom Cut Wood to learn more.
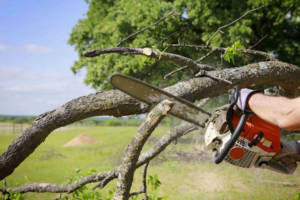
Woodworking is a complex art that requires skill and precision. It involves various cuts that shape and size lumber into functional and artistic pieces. Understanding different cuts can help you make the right decisions for your project. Some cuts are more important than others and can influence everything from structural integrity to aesthetic appeal. Fortunately, various tools and cutters are available that can cut wood to the desired length. These include miter saws, jigsaws, and circular saws. Choosing the right tool for your project will depend on the type of cut and desired finish.
Crosscutting is the process of cutting across the wood grain. This is a more difficult and time-consuming process than rip cutting, which cuts along the wood grain. Using the right blade for the job is also critical. Crosscutting blades typically have more teeth than rip cutting blades and offer a smoother finish.
Using the right blade will also minimize heat from friction, which can burn the wood during cutting. It is also important to cut slowly and carefully. Cutting too quickly can result in uneven or rough edges. It’s best to use a circular saw with a slow speed setting. This will reduce the likelihood of making mistakes and damaging your wood.
Many home improvement stores offer free wood cutting services. However, it is best to get your wood custom cut by professionals. This will ensure clean, accurate cuts and save you money in the long run. Inexpertly cut lumber can lead to damaged or inaccurate wood pieces that require more costly repairs. It can also waste valuable natural resources by creating rough edges that don’t look nice and won’t hold up well over time.
Rip Cut
Rip cutting is done by sawing along the wood grain to produce a thinner piece of lumber. It is a common cut in carpentry for making moldings that require precise dimensions. Generally, rip cuts are made with thin-kerf blades to help define the size of the cut accurately. Rip cuts are also made with gang rip saws, table saws, frame saws, some of which are whipsaws, and panel or hand saws.
To make a good rip cut, you must use the right kind of saw blade. Rip blades have a low tooth count and large gullets to clear away the saw chips. The teeth themselves have small, squared-off corners to help scrape the board as it is ripped through the kerf. This helps to prevent the saw from damaging the fibers of the wood. Rip blades are not suitable for cross cutting, as they will get caught in the wood fibers and won’t cut smoothly.
If you’re planning to rip custom cut wood for a project, consider using a rip fence attachment for your saw. This can help you achieve straighter and more accurate cuts by referencing the edge of the long piece to a short one for reference. This will give you more precision than just using a standard circular saw guide, which is not designed for this kind of work.
You can also buy a ripping jig for your saw that will clamp to the side of your workpiece and allow you to rip with great accuracy. These jigs are available from a number of different companies, and they can be very affordable. They are a great choice for anyone who wants to rip a lot of custom cut wood at once, saving time and effort.
Miter Cut
A miter cut is a type of angle used in woodworking to join two pieces together. It is commonly used to create picture frames or other decorative wood projects. The angled edge of a miter cut provides strength and improves the aesthetics of a finished project. Miter cuts can be made using a saw or a jig. It is important to choose the correct cutting method for your materials. Different cutting techniques are designed for different types of wood and other materials.
When making a miter cut, it is essential to use the right tools and measure carefully. A miscalculation can result in a piece that doesn’t fit together or visible gaps at the joints. To make sure you’re getting the best results, it’s a good idea to practice on scrap material. It is also a good idea to use a miter gauge, which helps you determine the angle of the blade.
Whether you’re installing baseboards or trim, it’s important to check the accuracy of your miter cuts before you nail them into place. A simple way to do this is by using a combination square. If the pieces fit tightly together, they are correctly positioned.
Miter cuts are a common part of carpentry and construction tasks, and they can add a decorative touch to any home improvement project. However, they can be tricky to master, especially for beginners. It takes training and practice to be able to set the required angle and create accurate cuts. Incorrect cuts can damage the material and lead to costly repairs or replacements. A professional who uses machine tools will make clean, precise cuts that limit wasted material and improve the look of your finished project.
Bevel Cut
Bevel cutting is an essential woodworking technique that gives your workpieces a polished appearance. It’s also a great way to strengthen joints that will be subjected to heavy loads. You can use a laser cutter to make bevel cuts on your workpieces. This method eliminates the need for manual grinding and is more efficient than traditional hand-held blades. This process is also safer and requires less maintenance. Besides being an efficient alternative, laser-cut bevel edges have a finer surface texture than traditional saw-tooth edges.
Depending on the type of material you’re working with, there are different types of bevels. Some bevels have angled corners, while others don’t. In the case of wood, there are several types of bevel cuts, including A bevel, X bevel, and V bevel. Each has a different angle and length that determines how the edge will look.
If you’re not familiar with bevel cutting, you can ask a professional to do it for you. This method ensures that you get clean and accurate cuts that will not damage or waste material. While professional cutting may cost more, it will save you money in the long run. Moreover, the results will be better than if you did it by yourself.
Unlike home DIYers, businesses cannot find all the lumber they need at local hardware stores. In fact, large companies need to procure wood fiber in truckloads per month. Since most sawmills only produce standard lumber dimensions in bulk, the only option for a business is to turn to industrial lumber suppliers. These companies have the equipment and expertise to provide businesses with custom cut woods. These woods will be more expensive than those from a retail store, but they will have superior durability and longevity.
Plywood
Plywood is a highly versatile material that can be used for a wide range of projects. Its lightweight construction makes it ideal for reducing building costs while also offering strength and durability. It is available in a variety of thicknesses and can be cut to length using a circular saw, handsaw, or jigsaw. It’s important to use proper safety equipment when cutting plywood, including a face mask and eye protection.
Custom cut plywood can play a crucial role in construction projects, enhancing the design while providing structural integrity. It can be used for everything from framing and sheathing to interior wall linings, floor and roof decking, and more.
Commercial businesses often turn to custom cut wood to create engaging and welcoming environments for customers. It can be used to create unique furniture and shelving that reflects brand identity and complements natural surroundings. In addition, it can be used for directional signage and bespoke display elements that enhance customer experience.
When choosing custom cut wood for a specific project, it’s important to consider the intended usage and how long the piece will be in service. For example, two-sided plywood is a popular choice for cabinets because it offers increased structural stability and durability. It can be purchased in a wide array of colors and finishes to enhance the appearance of any space.
While it is possible to cut plywood at home with a saw, it can be difficult for those without extensive woodworking or carpentry experience. The most efficient way to obtain custom cut wood is to work with an experienced lumber supplier. A professional can ensure that the finished product meets all specifications, reducing costs and cutting project times.